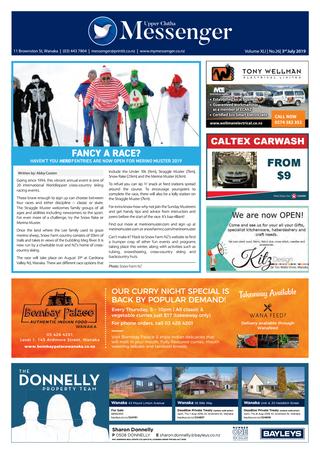
Understanding the design process for custom metal buildings
By Barry Clifton
When shopping for a new business suit, you have two choices: off the rack or tailored. Although it’s possible to walk into a store and find an acceptable standard size and style, often the best fit and look for you will require custom tailoring.
Such is the case when building a new facility for your mini-storage business. You could find the perfect building among a supplier’s hundreds of standard offerings, yet your particular business needs might require having a building designed to your specifications. If your plans call for a metal building, the custom design process is straight forward. To streamline the process so you can get your business up and running sooner, following are key points to keep in mind.
Standard building or custom?
The key to understanding whether to purchase a standard or custom building, is to first carefully consider the market segment your mini-storage business will focus on. A custom metal building enables effective targeting of your facility to suit customers’ needs.
For example, if your business is near camping or recreational areas, you might want to consider offering units large enough to store ATVs, camper trailers or boats. If you’re located in an urban area, there is typically a greater need to have more smaller units available.
Your building’s aesthetics are also a factor when deciding on a custom or off-the-shelf facility. Custom designs offer a much greater range of options, including metal color and/or finish surfacing applied to the units (such as stone, brick or stucco).
A custom design might also be appropriate given your site’s particular layout. Specifically, the configuration of the building(s) and door placement could need to be tailored for accessibility to driveways and interior circulation roads.
When to get started
As with many other things in life, the sooner you start the custom metal building design process, the better. A rough estimate can be obtained in as little as two days to two weeks, depending on the building complexity.
Contacting the building supplier early can help you determine the project’s feasibility. They can provide a rough plan that you can use to help in conversations with the local building department on permitting needs, and with your banker for financing. Later, the building plans can be finalized based on permitting and other requirements.
Information to have in hand
You don’t need to know all of the details of your project before contacting a supplier to discuss metal building options, but the key information to have in hand that will allow them to serve you better is:
- Planned number and sizes of storage units
- Types of storage needs to be served, such as
- General household items
- Business documents
- Larger items like vehicles, boats and RVs
- Desired building width, length and eave height (e.g., height of the exterior wall, not interior clear height under the roof); A rough idea of the building dimensions is sufficient at this point, as final size is sometimes determined by the desired unit mix
- Will the building(s) be climate controlled (for heated/air conditioned facilities, doors open to interior hallways rather than directly to the outdoors, which influences how the designer will configure your building)
- Lot dimensions and slopes
- Location of road access points
- Layout of any existing on-site roadways that will be retained, and thus constrain building size and placement
- Whether the building(s) will be visible from any major roads or highways, which can impact aesthetic requirements
- Availability and locations of utilities on site (if providing lighting, sewer, offices or washrooms)
Additionally, making a quick call to your local building department can provide you with some important up-front planning and permitting requirements. Ask them about:
- Whether the planned use is allowed under existing zoning or will require a zoning amendment, and zoning impacts on building design (such as for finishes, varied facades, and and size limitations)
- Property line setbacks
- Local building code requirements for mini-storage and metal buildings
- Snow load and wind load requirements for your region
Other details will arise as the building permitting and design process proceeds, but the above info is enough to get an initial design underway with your metal building supplier.
Custom design options to be aware of
Metal building suppliers offer a host of options for customizing your mini-storage building. Common items include:
Building trim, finishes and colors: Building owners can chose from a wide range of options for fascia, canopies and trim for an attractive finish, as well as rain gutters and downspouts to keep water away from the building. Additionally, suppliers produce metal wall and roof panels in numerous colors, along with gray tones and white.
Insulation: For non-climate controlled mini-storage buildings, a vapor barrier in the roof is typically sufficient to reduce condensation. In climate controlled facilities, suppliers can provide insulation for the roof and exterior walls, as well as between climate-controlled and non-climate-controlled portions of the building.
Interior partition placement: Interior walls that run the length of the building may be relocated in most instances to meet changing storage facility needs, while the partitions that transverse the width of the building are normally fixed.
Exterior door sizes, types and placements: Metal building suppliers can work with you to determine which door sizes and locations are appropriate for your planned storage needs. This can include sizing and placing overhead doors for vehicle and large item storage, versus walk-through doors for units that will hold common household items.
Door locks: Standard latches for doors on mini-storage facilities require padlocks. Some customers prefer cylinder locks, though, in which case you’ll need to discuss this with the building supplier as doors must be ordered to accommodate that lock type.
Windows: Although many mini-storage units do not include windows, you might want windows in some building areas, especially offices or other spaces serving customers. The building designer will need to account for window openings within the structural frame.
Costs
Both off-the-shelf and custom-designed metal buildings are economical. Your supplier should be able to provide an estimate early in the design process and a detailed quote before starting fabrication, so you can determine if the project will fit your budget. Metal buildings are typically lower cost than other standard construction types, plus are durable and easy to clean and maintain, which helps save costs over time.
Making the right choice for you
Similar to selecting the right tailor for a new business suit, it’s important to do your homework when choosing a metal building supplier. Ask for references, and if possible, visit mini-storage businesses that have used their products to get ideas for how the buildings could work for you. It’s also crucial to find out how long the supplier has been in business. A company with decades of experience is more likely to have the expertise to meet your building needs efficiently, cost effectively and with high quality.
Barry Clifton is the Sales Manager for Heritage Building Systems. The company is a full-service steel building manufacturer with more than 30 years of expertise in steel buildings, including custom designs for mini-storage and other facilities. www.heritagebuildings.com,
(800)-643-5555